In the past two years, the 3C electronics industry has developed rapidly, which has not only attracted careful defense from foreign enterprises, but also provided new opportunities for many domestic industry enterprises.
Taking the most popular mobile phone industry as an example, currently China’s mobile phone manufacturing giants are Foxconn, Huawei, and others. They are interested in investing in more intelligent manufacturing equipment. However, due to the cycle nature and production process requirements of mobile phones and other products, some existing equipment is difficult to comprehensively, completely, and cost-effective replace manual labor. Therefore, the application and transformation potential of automation in the 3C electronics industry is enormous, and there is great room for improvement.
In recent years, the smartphone industry has developed very rapidly. From single core to ten core processors (although the overall performance of ten core processors may not be the most impressive), the screen has also skyrocketed to 4K resolution, and curved screens, cameras can easily reach 20 million pixels, even 41 million pixels, as well as a series of hardware technologies such as fingerprint recognition and HiFi, which have been greatly improved. Hongzhan believes that the current mobile phone black technology is also becoming more and more impressive and more dreamy.
5G network fully deployed
With the rapid development of the economy and the continuous improvement of product process requirements in the manufacturing industry, the automatic dispensing machine, as an important component of it, has gradually become the main equipment of the process. Its importance is beyond doubt, not only saving costs for enterprises, improving product quality and production efficiency, but also starting to bid farewell to the traditional manual dispensing operation method. However, in daily use, various problems arise after prolonged use. So we have compiled and summarized the common problems and solutions of automatic dispensing machines, making it convenient for everyone to proficiently use automatic dispensing machines in their daily work.
First, let’s get to know the dispensing machine
Usually, dispensing machines, also known as dispensing machines, gluing machines, dripping machines, gluing machines, etc., are automated machines that specifically control fluids and apply them to the surface or interior of products. The dispensing machine is mainly used to accurately point, inject, apply, and drip glue, paint, and other liquids in the product process to the precise position of each product. It can be used to achieve dot, line, circular or arc shapes.
Analysis of dispensing principle
Valve body exploded view
1. Under the action of feed pressure, the fluid fills the cavity flow channel;
2. Open the solenoid valve, compress air into the valve body, and push the striker assembly upward until it contacts the lower end of the stroke adjustment rod. The striker assembly rises at a distance of h (note: h is an adjustable variable controlled by the stroke adjustment assembly); And stay at this position for an appropriate period of time, at which point the striker separates from the nozzle pad, and the fluid enters the nozzle impact seat;
3. Close the solenoid valve, and under the action of the pre tightening force, the striker quickly impacts the nozzle seat, converting the pre pressure potential energy of the spring into the kinetic energy of the striker component’s downward movement. The fluid is quickly cut off during the flow process, and at the moment of closure, the fluid is sprayed out as a droplet through the nozzle.
Application case diagram
Factors for precise glue control
Commonly applicable liquid glue
Various solvents, adhesives, paints, chemical materials, solid adhesives, etc., including silicone, EMI conductive adhesive, UV adhesive, AB adhesive, quick drying adhesive, epoxy adhesive, sealant, hot adhesive, lubricating grease, silver adhesive, red adhesive, solder paste, heat dissipation paste, anti solder paste, transparent paint, screw fixing agent, woodworking adhesive, anaerobic adhesive, acrylic adhesive, anti wear adhesive, crystal adhesive, pouring adhesive, horn adhesive, instant adhesive, rubber, paint, enamel paint, varnish, ink Pigments, etc.
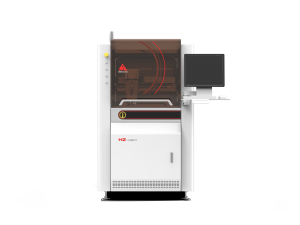
As an automated dispensing device, automatic dispensing machines are widely used in industries such as electronic smartphones, lighting, automotive, industrial electrical, and solar photovoltaic. The most common problem encountered by automatic dispensing machines is valve problems. The following are effective methods to solve the problems that often occur when using glue valves:
1. Rubber nozzle blockage
Reason: The needle hole of the automatic dispensing machine is not completely cleaned, impurities are mixed in the adhesive, there is blockage phenomenon, and incompatible glue is mixed, resulting in less or no glue points coming out of the nozzle.
Solution: Replace with a clean needle and a high-quality patch adhesive. The patch adhesive brand should not be mistaken.
2. Rubber valve dripping
Reason: The diameter of the needle used in the dispensing machine is too small. A needle that is too small can affect the exhaust bubble action of the glue valve when it starts to use, affecting the flow of liquid and causing back pressure. As a result, the phenomenon of dripping and leakage occurs shortly after the glue valve is closed.
Solution: Simply replace the larger needle to solve this problem. In addition, the air in the liquid may cause dripping and leakage after the rubber valve is closed. It is best to exclude the air in the liquid in advance, or use glue that is not easy to contain bubbles, or centrifuge the glue before use.
3. Flow rate too slow
Reason: The dispensing machine pipeline is too long or too narrow, the air pressure at the nozzle is insufficient, and the dispensing flow rate is too slow.
Solution: Change the dispensing machine pipeline from 1/4 “to 3/8”. If there is no need, the pipeline should be as short as possible. In addition, it is necessary to improve the adhesive port and air pressure, so as to accelerate the flow rate.
4. Bubbles in the fluid
Reason: Due to excessive fluid pressure and short valve opening time, the dispensing machine may penetrate air into the liquid, causing the generation of bubbles.
Solution: Reduce fluid pressure and use a conical inclined needle.
5. Inconsistent glue size
Reason: The pressure cylinder or air pressure of the dispensing machine storing fluid is unstable, resulting in uneven dispensing and inconsistent size.
Solution: Avoid using the low pressure part of the pressure gauge. The control pressure of the glue valve should be at least 60psi or above to ensure stable glue output. Finally, the adhesive release time should be checked. If it is less than 15/1000 seconds, it will cause unstable adhesive release. The longer the adhesive release time, the more stable the adhesive release.
How to solve the problem of wire drawing when using adhesive with high viscosity in automatic dispensing machines
In general, low viscosity glue is often used for large-scale applications, such as film covering, sealing, and large area bonding. Medium viscosity glue is easy to operate and is suitable for most bonding, sealing, and other operations. High viscosity glue is difficult to dispense, has weak or almost no fluidity, and is suitable for cofferdams, reinforcement, and other applications. Some products require the use of high viscosity adhesive due to process requirements. During the dispensing process, due to the high viscosity, sometimes wire drawing occurs, which affects the quality and aesthetics of the dispensing. So, how to solve the problem of wire drawing?
Complete solution:
If the company has very strict requirements for product quality, it can be considered from the hardware aspect. The dispensing valve is equipped with valves specifically designed for high viscosity fluids, such as imported screw valves. The viscosity value of the glue is provided to the manufacturer, and the manufacturer will help you type according to the viscosity value of the glue to achieve perfect dispensing effect. Of course, for high viscosity screw valves, the price may be relatively expensive, but it perfectly solves the problem of wire drawing.
Other solutions:
1. Glue opening delay
When opening the glue head, there is a distance between the glue outlet of the glue head and the glue valve, and there is no glue between this distance. If the glue output port of the glue head is opened and immediately starts to move, it will cause a small section of the trajectory to lack glue. To prevent this situation, after opening the glue, delay for a period of time, wait for the glue to flow out, and then perform subsequent movements. This delay time is called the glue opening delay.
2. Closing glue delay
After closing the glue head, there is still glue between the glue outlet of the glue head and the glue valve that has not run out. If the glue head moves immediately after closing, it may form a phenomenon of glue dragging. To prevent occurrence, after closing the glue head, delay for a period of time until the glue has finished flowing, and then perform subsequent actions. This delay time is called the glue off delay.
3. Wire drawing height
Due to the high viscosity of certain adhesives, it is necessary to slowly raise them at a constant speed for a certain distance to break the adhesive wire, without affecting the coating trajectory. This distance is called the drawing height.
4. Lifting height
When a segment of the trajectory ends dispensing and moves empty to the starting point of the next trajectory, in order to prevent the glue head from hitting the needle, the glue head is raised a certain height at the end point to ensure the safety of the glue head from hitting the needle, and then moves empty to the starting point of the next trajectory. This height is called the lifting height.
5. Close the glue in advance
Early closing of adhesive “refers to the distance of early closing of adhesive, which refers to the process of closing the adhesive head before reaching the end point in a continuous trajectory of adhesive application, and completing the final trajectory with residual pressure and adhesive to avoid stacking adhesive at the end. The length of this trajectory is called the “glue off distance”.
6. End Action
After the dispensing of glue on the entire teaching trajectory is completed, in order to facilitate the retrieval and placement of workpieces, improve processing efficiency, or eliminate processing errors, users can set the glue head to move to the designated position, or the starting point of the processing file, or the end point of the processing file, or reset, or perform file connection. This project is called the end action.
7. Diagonal lifting
Due to the viscosity of the adhesive, direct wire drawing after closing the adhesive cannot achieve the effect of breaking the adhesive wire, or the shape of the pulled adhesive wire does not meet the requirements. Therefore, after closing the rubber head, perform a diagonal pull up movement as preparation for wire drawing
8. Glue heating
You can try heating the glue to a suitable temperature to increase its fluidity, and it can also solve the problem of wire drawing in a sense! Please note that the heating temperature should not be too high!
The influence of dispensing height on precise glue control
The above content is Hongzhan’s understanding of the common faults and solutions of automatic dispensing machines. I believe everyone has a better understanding. The common problems with automatic dispensing machines can be large or small, and users can quickly solve these problems as long as they master the correct solutions.