Due to the price increase of raw materials for lithium-ion power batteries, nearly 40 major models of nearly 20 new energy vehicle brands in China have seen a surge since March 2022, with some car companies experiencing several consecutive increases this year. Ideal ONE insisted on not raising prices on March 20th and also announced an increase in prices on its official Weibo account on March 23rd.
How is the price of raw materials rising?
As the cost leader of new energy vehicles, the prices of raw materials such as lithium, cobalt, and nickel for power batteries are all significantly increasing. At present, the domestic quotation for battery grade cobalt is 568500 yuan/ton, which is nearly three times higher than the beginning of 2021; The price of lithium carbonate was reported at 504000 yuan/ton, an increase of 73.8% compared to the beginning of the year and a year-on-year increase of 479.3%.
What has pushed up the price of lithium batteries?
1. there is a significant increase in demand for power lithium batteries.
Since 2017, the rapid growth in sales of new energy vehicles has driven an increase in the number of power battery installations. New energy vehicles are becoming increasingly popular among Chinese people, and major domestic new energy vehicle companies are also driving overall demand to seize the market share of their brands.
2. The import of mineral raw materials is in short supply, resulting in a shortage of supply.
Global lithium mines are mainly distributed in countries such as Chile, Australia, Argentina, Bolivia, etc. Cobalt mines are concentrated in countries such as the Democratic Republic of Congo, Indonesia, and Australia, while nickel mines are concentrated in countries such as Australia and Russia. The monopoly of the COVID-19 and Toutou Mining Group is also an important reason for driving up prices.
High battery scrap rate and high cost
In addition to the cost of raw materials, the scrapping of battery cells caused by overlapping loading in the assembly process of battery cells is also a major reason for driving up costs. The production of a lithium battery requires approximately 60 to 140 cycles of positive and negative electrode stacking, and repeated loading of one cycle can result in the cell being scrapped, resulting in extremely strict production requirements.
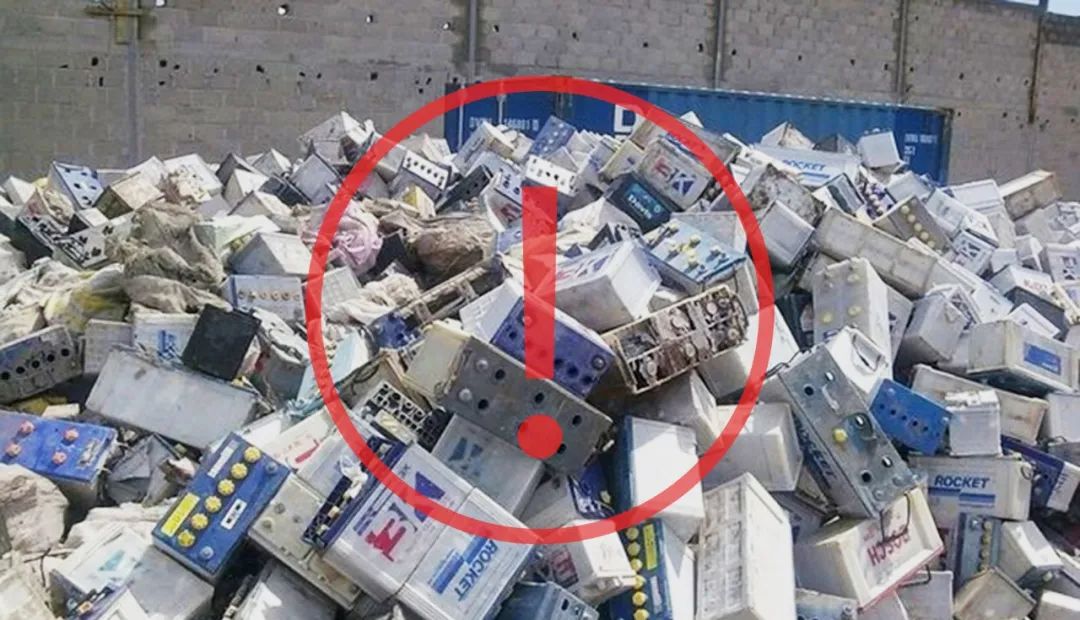
Battery scrap – battery cell scrap piled up in a mountain
A certain lithium battery manufacturer has a defect rate of up to 2.14% caused by repeated laminations. Not only is cost consumption severe, but it even affects the delivery time of orders.
Due to the susceptibility of negative pressure between the electrode plates and the electrode ear plates to stacking, even if they add a shaking process during feeding, it is difficult to suppress the occurrence of stacking problems.
Due to the characteristics of “light”, “small”, and “thin” metal sheet materials in the lithium battery industry, some commonly used dual sheet detectors on the market often fail to meet the process requirements of the lithium battery industry, resulting in frequent false alarms and missed reports of dual sheet materials.